Benefits of Inflatable Fenders: Key Advantages for Maritime Safety
04/16/2025Berth Fender Classification: Key Types and Applications
04/18/2025Arch Rubber Fender: A Robust Solution for Marine Protection
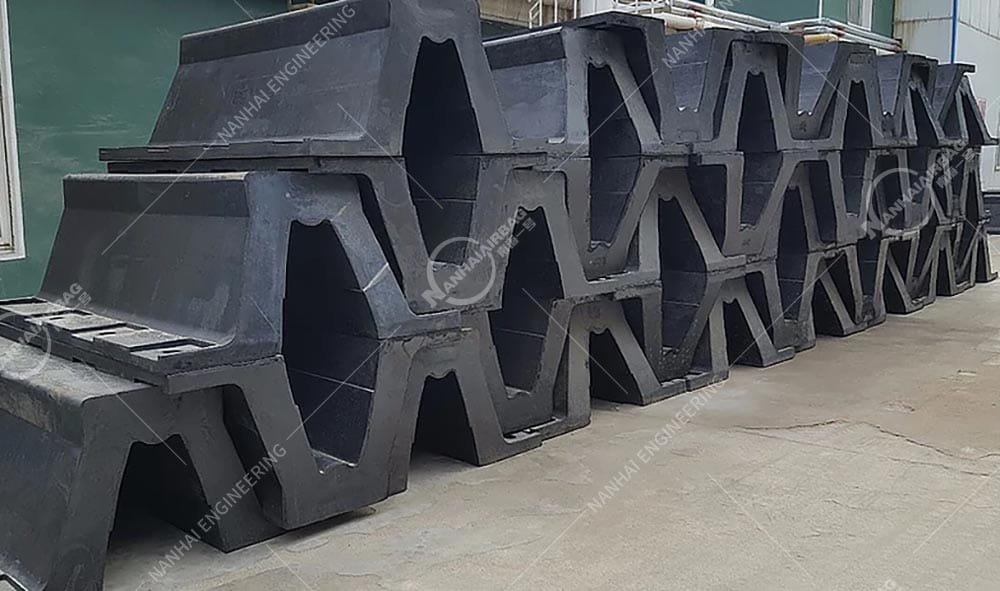
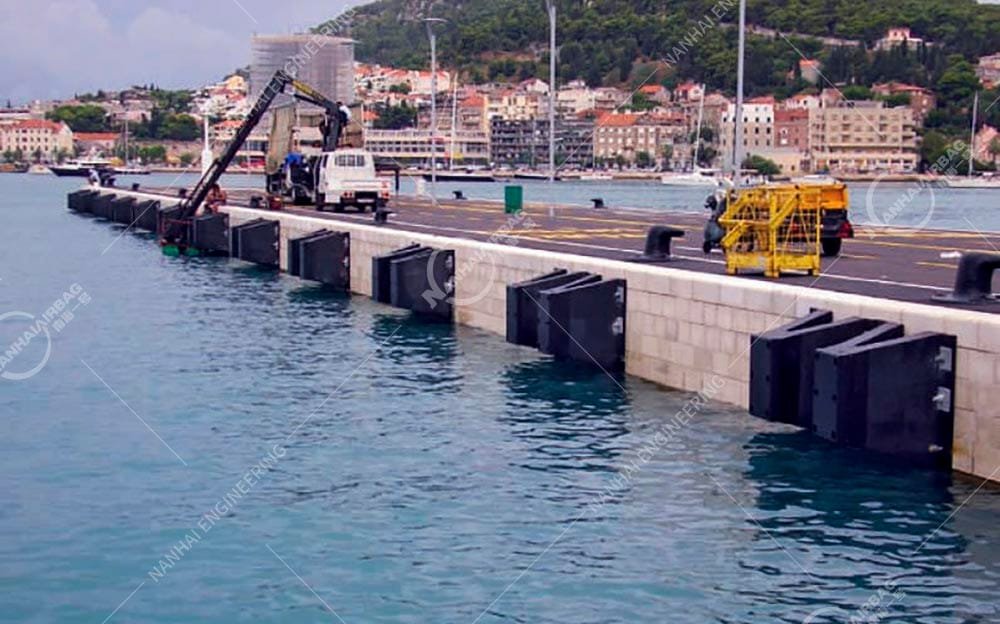
Arch Rubber Fenders are critical components in marine infrastructure, designed to absorb impact energy during ship berthing, mooring, and cargo operations. Combining engineering precision with high-performance rubber materials, these fenders are widely used in ports, harbors, and offshore platforms. Below is a detailed introduction to their design, functionality, and advantages.
1. What is an Arch Rubber Fender?
An Arch Rubber Fender is a cylindrical or arched-shaped rubber structure mounted on docks, quays, or ships to protect both vessels and shore infrastructure from collisions. Its iconic “arch” design distributes impact forces evenly, reducing localized stress and preventing structural damage.
Key Components:
- Rubber Body: Made from high-quality natural or synthetic rubber compounded with reinforcing fibers (e.g., nylon, polyester) for durability.
- Steel Reinforcement: Internal steel rings or helical wires embedded to enhance load-bearing capacity and prevent deformation.
- Mounting System: Bolted or welded to quay walls or vessel hulls, ensuring secure installation.
2. How Does It Work?
The arch shape plays a pivotal role in energy absorption:
- Energy Dissipation: When a ship collides with the fender, the arch structure deforms elastically, converting kinetic energy into heat through rubber compression and friction.
- Force Distribution: The curved profile spreads impact forces across a larger surface area, minimizing stress concentration on the vessel or dock.
Performance Metrics:
- Energy Absorption: Up to 200–500 kJ/m³, suitable for vessels ranging from small ferries to large container ships (e.g., 15,000–20,000 TEU).
- Reaction Force: Controlled rebound ensures minimal “snubbing” effect, reducing ship movement during mooring.
3. Core Advantages of Arch Rubber Fenders
Superior Impact Resistance
- Outperforms traditional wooden or foam-filled fenders in harsh conditions.
- Withstands repeated collisions without permanent deformation, ideal for high-traffic ports like Shanghai Yangshan or Rotterdam.
Durability in Extreme Environments
- Resistant to saltwater corrosion, UV radiation, and temperature fluctuations (-30°C to +80°C).
- No risk of leaks or pollution, unlike foam-filled fenders that degrade over time.
Cost-Effective Maintenance
- Minimal upkeep required; periodic inspections and cleaning suffice.
- Long lifespan (20+ years), reducing replacement costs.
Versatile Applications
- Ships: Protects hulls during berthing and cargo handling.
- Ports: Safeguards quay walls and quay cranes from vessel impacts.
- Offshore: Used in oil rigs, LNG terminals, and floating wind farms.
Compatibility with Modern Ports
- Works seamlessly with automated mooring systems and smart port technologies.
4. Types of Arch Rubber Fenders
- Standard Arch Fenders: General-purpose use in medium-sized ports.
- Reinforced Arch Fenders: Feature extra steel layers for mega-ships (e.g., VLCC tankers).
- Custom Designs: Tailored shapes and sizes for specialized applications (e.g., floating docks).
5. Real-World Applications
- Shanghai Yangshan Deep-Water Port: Arch fenders protect berths handling 20,000-TEU container ships.
- Port of Rotterdam: Deployed in oil terminal quays to mitigate collisions from VLCCs.
- Arctic Offshore Platforms: Specialized fenders resist ice-induced impacts.
6. Future Developments
- Smart Fenders: Integration of IoT sensors to monitor collision forces and predict maintenance needs.
- Recyclable Materials: Bio-based rubber compounds to meet circular economy goals.
- Hybrid Designs: Combining rubber with composite materials for lighter, high-strength fenders.
Conclusion
Arch Rubber Fenders remain a cornerstone of marine safety due to their unmatched durability, energy absorption efficiency, and adaptability. As global shipping grows and ports modernize, these fenders will continue to evolve, integrating smart technologies and sustainable materials to meet the demands of safer, greener, and more efficient maritime operations.