Inflatable Fender’s Repairing
12/02/2024Repairing A Ship Launching Airbag
12/04/2024Marine Airbag’s Production Process
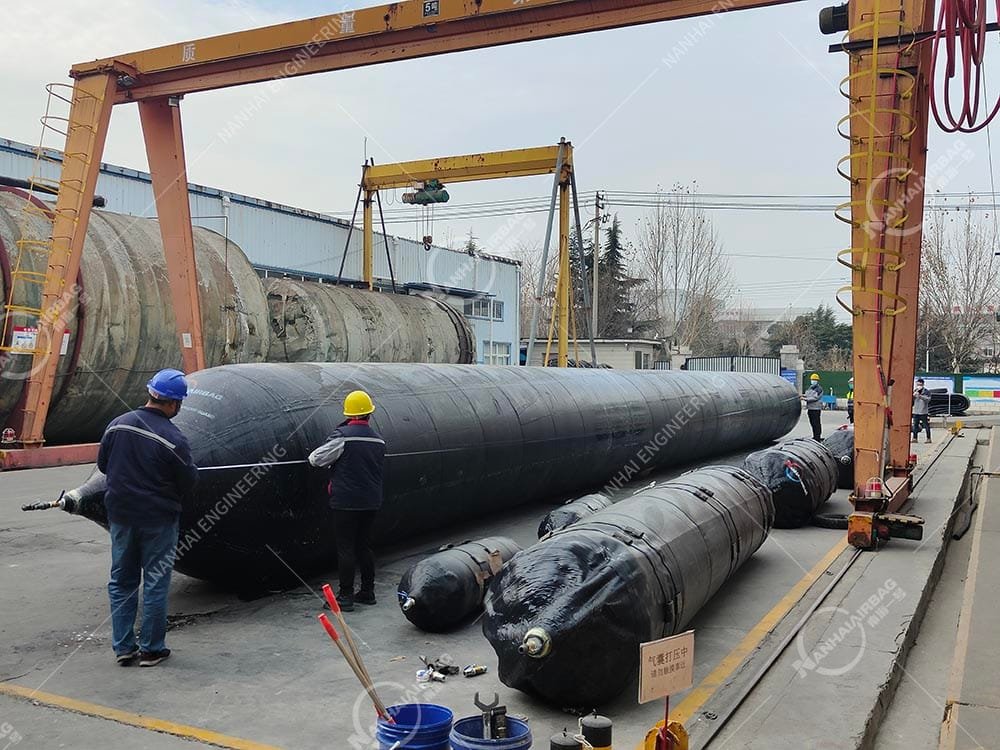
A marine airbag is a pneumatic buoyancy device used for ships, offshore platforms, and other maritime applications. It is commonly used for functions such as rescue, lifting, support, or transportation. The manufacturing process of a marine airbag involves several production stages to ensure it has adequate pressure resistance, corrosion resistance, aging resistance, and good airtightness. Below is the main production process of a marine airbag:
1. Material Selection
Marine airbags are typically made from high-strength synthetic rubber, PVC (polyvinyl chloride), or other polymers resistant to seawater corrosion. The materials need to have the following characteristics:
- Pressure resistance: To withstand the pressure changes during the sinking and floating of the ship.
- Aging resistance: To maintain a long service life under UV radiation, seawater, and temperature fluctuations.
- Corrosion resistance: To resist corrosion from seawater and other corrosive substances.
- Airtightness: To ensure that the airbag does not leak air after being inflated.
2. Material Preparation and Cutting
- Select suitable synthetic rubber or PVC sheets and cut them according to the specifications of the airbag. The materials are usually cut into circular or elliptical sheet shapes based on the size of the airbag.
- The thickness and specifications of the materials are determined by the airbag’s working pressure and the intended use environment.
3. Molding Process
- Vulcanization: The cut materials are heated and pressurized to undergo a vulcanization reaction, which forms a high-strength rubber material. Vulcanization enhances the material’s elasticity, heat resistance, and aging resistance.
- High-frequency welding: High-frequency electrical current is used to weld the materials together, forming the basic structure of the airbag. The welding technique ensures seamless connections between different parts (such as the main body and connectors), preventing air leakage.
4. Production of Inflation and Deflation Ports
- Inflation Port: An inflation valve is installed on one side of the airbag to facilitate air inflow. The inflation port is designed with a structure that prevents air leakage, typically using threaded or snap-fit designs to ensure airtightness during inflation.
- Deflation Port: According to design requirements, the deflation port is used to release air from the airbag. In some high-performance airbags, the deflation port is designed to control airflow, ensuring safety and effectiveness when releasing air.
5. Sealing Treatment
- After welding the airbag, a sealing test is performed. Common testing methods include checking for air bubbles on the surface of the airbag after inflation, using a pressure gauge to test the internal pressure changes, etc.
- Sealing the joints and welded areas is crucial to ensure that the airbag does not leak air during use.